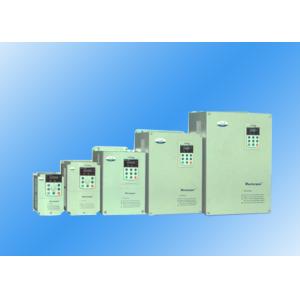
Add to Cart
Vector Control and Dynamics of AC Drives VSD for Extrusion Machines
Extrusion machines are used to create product by forcing raw material, such as plastic, through a die. Extruders are used to create a wide range of products such as tubing, sheet goods, and insulation. Food processing is a popular application for extruders. Extruders employ a main drive motor to supply power to a screw, which provides the force necessary to push the raw material through the die.
Application Challenges
· Replace hydraulically operated or DC powered drives
· Precise speed control while material is being extruded
· Develop high torque at very low speeds
Features of V5 series matching lift control application
Item |
Features |
Excellent Control Performance under Speed Sensorless Vector Control Mode |
The bus voltage is under stable control. Quick and reliable braking can be realized when decelerating under the condition of braking without power consumption.
|
Realizing Real Tripless Operation |
|
Unique Instantaneous Mains Failure Reaction |
|
Unique Speed Tracing Function |
|
Unique Quick DC Braking |
|
Power range of V5 VFD
Voltage: 3 phase 380VAC (323VAC – 528VAC)
Power: 1.5kw/2HP – 400kw/535HP
Specification of V5 VFD
Item |
Specification |
Input frequency |
50/60Hz |
Output frequency |
0-300Hz |
Overload current |
150% rated current 1min., 180% 10 sec., 200% 0.5 sec. |
Control mode |
sensor-less vector control, V/F control |
Starting torque |
180% 0.5Hz (180% 0.25Hz) |
Control precision |
±0.05% ( ±0.02%) |
Torque precision |
±5% |
Frequency setting mode |
Operation panel setting, terminal UP/DN setting, host computer communication setting, analog setting AI1/AI2/AI3, terminal pulse DI setting |
Efficiency |
At rated power, 7.5kW and below power class ≥93%, 45kW and below power class ≥95%, 55kW and above power class ≥98% |
Frequency setting signal |
-10V~+10V; 0~+10V; 0~20mA; 0.2Hz~50kHz |
Protection function |
Power supply undervoltage, overcurrent protection, overvoltage protection, interference protection, abnormal comparison reference input, auto-tuning failure, module protection, heatsink overtemperature protection, inverter overload protection, motor overload protection, peripheral protection, abnormal current detection, output to ground short circuit, abnormal power failure during operation, abnormal input power, output phase failure, abnormal EEPROM, abnormal relay contact, temperature sampling disconnection, encoder disconnection, abnormal +10V power supply output, abnormal analog input, motor overtemperature (PTC), abnormal communication, abnormal version compatibility, abnormal copying, abnormal expansion card connection, terminal mutual exclusion detection failure, hardware overload protection |
Enclosure |
IP20 |
Cooling mode |
forced air cooling |
Vibration |
3.5mm, 2~9Hz; 10 m/s2, 9~200Hz |
Ambient temperature / Humidity |
-40 Degrees~+70 Degrees / 5~95%Rh (no condensation) |
Tips:
A variable-frequency drive (VFD) is a system for controlling the rotational speed of an alternating current (AC) electric motor by controlling the frequency of the electrical power supplied to the motor. A variable frequency drive is a specific type of adjustable-speed drive. Variable-frequency drives are also known as adjustable-frequency drives (AFD), variable-speed drives (VSD), AC drives, microdrives or inverter drives. Since the voltage is varied along with frequency, these are sometimes also called VVVF (variable voltage variable frequency) drives.